Home » Industry Analysis » Solar Market Capacity Analysis
Solar Market Capacity Analysis
The global solar energy market is in a stage of rapid growth, mainly due to various factors. First, the cost of solar technology has dropped significantly, making solar energy an economically viable energy option in many countries and regions. Second, there is increasing global demand for renewable energy, especially in combating climate change and reducing greenhouse gas emissions. In addition, many countries realize that developing clean energy is not only an effective way to deal with climate change but also a long-term solution to energy security issues.
According to the World Energy Investment Report released by the International Energy Agency, global energy investment is expected to reach approximately US$2.8 trillion by 2023. Investment in the solar energy industry is expected to surpass oil for the first time in 2023, reaching US$380 billion, while investment in oil production is expected to be US$370 billion. This suggests that the gap between investment in clean energy and investment in fossil fuels will grow wider.
In Greece, which is rich in solar energy resources, the average annual sunshine hours are about 3,000 hours, and the average annual solar radiation is 1,400-1,800 kWh/ square meter. The Greek government actively promotes solar power generation and promotes the development of the solar industry through the implementation of ecological island plans and other measures. Hellenic Petroleum invested 130 million euros to build a photovoltaic park with an installed capacity of 204 MW in Kozani, becoming one of the largest solar power projects in the Eastern Mediterranean.
The Asia-Pacific region is expected to dominate the solar energy market during the forecast period as countries such as China, India, and Japan implement ambitious renewable energy targets and support policies such as feed-in tariffs, renewable portfolio standards, and subsidies for solar installations. In addition, some countries in the Asia-Pacific region have embarked on ambitious large-scale solar projects, such as China's utility-scale solar installations, which have increased the region's cumulative installed solar capacity and made it a dominant player in the global solar market.
However, rapid growth also faces a series of opportunities and challenges. According to the latest report, the world is actively expanding solar energy production capacity to meet the growing demand for green energy. While lower prices are good for consumers, they could lead to lower investment, raising the risk of future supply shortages. In particular, the demand for key minerals such as copper, lithium, nickel, cobalt, graphite, rare earths, etc. This is crucial for the production of solar cells.
World Wide PV Solar Growth
As can be seen from the chart (updated in July 2018) the solar industry has seen remarkable growth. The red bars represent the "annual" amount of PV solar systems installed by manufacturers in giga-watts (1 GW = 1 billion watts). For reference purposes, one nuclear reactor produces about 1.3 GW of electricity per year. The data for 2012 and 2013 is from the European Photovoltaic Industry Association (EPIA). The data for 2014 and 2015 is from Mercom Capital. The data for 2016 and 2017 is from CleanTechnica. The author created the overall graph.
The 5 year average growth rate from 2012 (30.1 GW) to 2017 (98.9 GW) was 29% per year - a very nice growth rate. The growth in 2015 was 28%, 2016 was 32%, and 2017 was also 29%. The overall 29% growth was mainly due to China and the US, which have grown nicely throughout this five year period.
The growth in 2014 of only 17% was because of sharp cutbacks in Germany and Italy. Also, China had no growth at all as they were consolidating their tremendous leap from the previous year. However, in 2016 China doubled to 34.5 GW - by far the largest yearly installation ever. In 2018 and afterward, the long-term growth rates are expected to be roughly 20% per year. While the overall five year growth rate is very impressive, the 98.9 gigawatts of new solar in 2017 was just 0.4% of the worldwide amount of electricity (25,551 GWh) generated by all sources. There were about 417 GW of cumulative PV solar installed worldwide at the end of 2017 compared to 318 GW at the end of 2016.
The installed PV base is roughly 20% residential rooftops, 20% commercial buildings like hotels and malls, and 60% utility plants connected to the grid. The utility market has really taken off in the last several years and is the market segment that has been the most influential in recent growth rates. The utility market is also the most cost-efficient segment as material, land, and labor costs can be spread over huge quantities.
Solar-generated electricity makes a substantial contribution during the time of day when lots of electricity is most needed, those hot summer afternoons when air conditioners are running almost constantly. This is when solar can add significant contributions to the grid at less cost than other sources. When you also throw in the pressure to go "green", you can see why the long-term future for this industry is very good.
PV Solar Installation by Country
The chart shows PV solar installed by the country in megawatts. Germany, back in 2012, had been the leader in solar power. Germany has a goal to discontinue all nuclear power by the year 2022 and replace it with renewable resources. However, as the price of solar power has decreased and Germany has been on target to meet its goals, they reduced their solar incentives. This prompted installations to peak in 2012 and fall off dramatically thereafter. (The same thing occurred in Italy from 2012 to 2015, not shown in the chart). In 2013 China, which has about 65% of the world's solar manufacturing capacity, began to focus on its own internal needs for clean power. It dramatically increased its solar power in 2015 and 2016. China is now the world leader in PV solar and will likely remain so for the foreseeable future. In the last several years the United States has come on strong with significant installations.
As can be seen in the chart above, the US previously had been behind in installations. In 2006 the US implemented the Renewable Energy Investment Tax Credit (ITC) which allows solar installations to apply 30% of the cost of design and installation as a federal tax credit with no maximum credit limit. The ITC was set to expire in 2016 (a 10 year program) but has been extended until 2021. In addition, a “commence construction” feature was added, effectively extending the policy through 2023.
There are 14 US States and the District of Columbia that regulate retail electricity markets in which customers may choose "alternative" power suppliers. States, such as California and Arizona, have implemented their own aggressive incentive programs to encourage alternative power. A "net-metering" type of arrangement has been implemented by California, Arizona, and many other states, whereby solar electricity is "sold back" to the utility. However, the total annual amount sold back to utilities can not exceed the customer's annual electricity usage times the purchase price.
Feed-In-Tariffs
Germany's nuclear reduction goal prompted a government policy called feed-in tariffs (FITs). A feed-in-tariff is a policy designed to encourage the adoption of renewable energy of all kinds to accelerate the reduction of the cost of renewables down to grid parity or less. Besides PV solar they include other technologies such as concentrated solar power (CSP), wind, and geothermal. FITs typically include three provisions:
In almost all of Africa, Pakistan, Hawaii, Italy, and large portions of Japan, the price of electricity is already in excess of what the cost of electricity is from solar. Therefore in these locations, there is a ready market for today's solar electricity without any subsidies. As the price of solar electricity continues to come down every year, more and more locations will benefit from making the switch to solar when new capacity is added.
Overcapacity Issues: 2011 to 2013
Between 2007 and 2011 the solar industry grew approximately 70% per year. In particular, from the major recession year of 2009 and the recovery year of 2010, the industry grew at an incredible 172%! Production was hard-pressed to keep up with demand. As a result, companies that were able to dramatically increased capacity and gained market share. No one wanted to be left out because of a lack of capacity. So every company added capacity as fast as they could, thinking the industry growth would continue for the foreseeable future. In 2010 industry analysts warned that too much capacity was being brought on stream. However, the market was growing at double the analyst's forecasted growth rate, so the added capacity was easily absorbed. Producers felt they were "smarter than the analysts"!
In early 2011 capacity additions finally began to exceed demand. Prices of crystalline silicon solar cells began to tumble as companies, especially second and third-tier companies, fought to reduce inventories that were piling up. In spite of the fact that the industry continued to grow at a 40% clip, there was so much inventory by the middle of the year that all prices - modules, cells, wafers, and polysilicon - tumbled uncontrollably.
For example, silicon wafer prices dropped about 70%, solar cells dropped about 60%, and modules dropped about 50%. GTM Research estimates that 31 GW of crystalline solar cells were produced. However, only about 25 GW of silicone cells were sold, leaving 6 GW of excess crystalline inventory, which was about 24% of the amount sold. Because of this glut, many smaller producers simply suspended manufacturing operations and one major company, Q-Cells of Germany, filed for bankruptcy. In the longer run the analysts were right.
The hardest hit were the polysilicon suppliers. Prices dropped from about $80/kg at the beginning of 2011 to about $20 at the end of 2011, a 75% drop. This happened because back in 2007 and 2008 there was a worldwide polysilicon shortage and polysilicon prices increased to about $400/kg. Suppliers made a lot of money and added tons of capacity so that there was a huge polysilicon capacity overhang estimated to be 40 GWs. The main reason crystalline silicon "cell" prices dropped by 60% in 2011 was because the raw material, polysilicon, which makes up a very significant part of the total cost, dropped so tremendously. While there was too much solar cell and module capacity, it was nowhere near as bad as polysilicon. Analysts believe solar cell and module capacity became reasonably in line by 2015, but the polysilicon glut took several more years to work off. As a result of falling prices while unit shipments increased, almost all companies in the solar industry were unprofitable from 2011 to 2013.
Those Chinese companies who had stock traded on American exchanges, and had to follow American accounting rules, mainly lost money because of inventory write-downs and other asset impairment write-downs. Most of these were non-cash items on balance sheets. Actual cash flows were not as negative as profits. Some companies even continued to have a positive cash flow. 2014 proved to be a profitable year for the companies that survived the 2011 through 2013 glut of products. This process was a good lesson that was learned by the entire industry.
Market Share by Technology
As can be easily seen from the chart, crystalline silicon dominates the solar market by a large margin. Thin film's share for all thin film technologies was about 7% in 2017 down from 18% in 2009. Crystalline Silicon's share has been rapidly increasing the last few years as Chinese manufacturers have come on strong.
The leader by far in thin film technology is First Solar whose cadmium telluride module manufacturing costs are somewhat less than those of most crystalline cell manufacturers. Crystalline wafers are about 200 microns (a micron = one millionth of a meter) thick. In contrast, thin-film panels are made by vacuum depositing several layers of semi-conductor materials only a few microns thick. Silicon in its pure form (99.9999% pure for solar applications) is very expensive and makes up about 20% to 25% of the cost of crystalline panels vs. the semiconductor cost of about 2% in thin film panels.
There are two types of crystalline silicon, mono-crystalline and multi-crystalline. The efficiency of thin film and multi-crystalline silicon are roughly the same. However, thin film panels are currently not as efficient as mono-crystalline panels, and therefore more thin film panels are required to generate the same amount of electricity. A thin film installation can take up to 25 percent more space (and land) to achieve the same total power output as a mono-crystalline installation. But, mono-crystalline panels are significantly more expensive than thin-film. This makes thin film strongest in the utility-scale market because the cost of panels outweighs the cost of land and labor in this market. First Solar, Sharp, and a few other manufacturers have had success with "thin film" in the utility market.
Chinese suppliers using multi-crystalline silicon have significantly reduced their costs and prices, and thus have gained market share. They operate on very thin margins and depend on large volumes to get their unit costs down. Of the ten top PV producers in 2017, nine were Chinese. The dramatic drop in silicon module prices from 2011 to 2017 has probably closed the cost gap between multi-crystalline silicon and cadmium telluride.
2017 Top 10 Solar PV Manufacturers Worldwide
Listed below are the top ten PV manufacturers for 2017. Companies are ranked by "megawatts shipped", not revenue. Nine of the top 10 PV producers are purely Chinese. During 2017 approximately 60% of all PV solar panels shipped were manufactured in China. (Note that Canadian Solar has a 500 MW manufacturing plant in Canada in addition to its main plant in China.) Jinko Solar is number one on the top 10 list, followed by Trina Solar and Canadian Solar. In the past three years, JinkoSolar, Trina Solar, and Canadian Solar have been the top 3 module suppliers in the solar industry, and by some margin. These companies offer something that no other module suppliers have: "global brand recognition".
Most companies try to completely vertically integrate, i.e. manufacture all three stages of production - wafers, cells, and modules. Wafer companies moved into cells because they have a cost advantage using their own wafers. Pure cell manufacturers have moved into modules, which are basically low-tech assemblies, but it also gives them a low-cost material advantage. Major players want to be totally integrated from wafers to modules and even end-user sales and installation. Having an internal supply of materials shields companies from the up-and-down swings of the spot markets and provides an opportunity to "brand" their products.
US PV Market Growth
This is the annual US PV solar installations in megawatts (MW). Note that during 2016 installations totaled 14,600 MW, a gigantic 83% increase from 8,000 in 2015.
As mentioned above, the ITC (Renewable Energy "Investment Tax Credit") was set to expire at the end of 2016 but during 2016 it was extended until 2021. Many organizations rushed their solar installations to take advantage of the ITC before the end of 2016. Therefore some of the installations scheduled for early 2017 were finished in 2016.
For a more balanced calculation of the five year growth rate, the average for both 2016 and 2017, i.e. 12,600 MW, was used for the ending year of 2017. The five year annual growth rate from 2012 to 2017 was 31% using the 12,600 MW average for 2017.
US solar installations have grown dramatically in the last few years as utilities have come on strong. Until about 2011, US utility installations had been weak compared to Germany, Italy, or China due to the lack of support from the US Federal Government in the early 2000s. The planning and licensing for a large utility installation takes a minimum of two to three years plus the time to install it. So the Investment Tax Credit (ITC) tax incentive program passed in 2006 took a while to have an effect. Also, in recent years, state governments added their support and those results began to show starting about 2013.
A 100 MW to 250 MW solar installation costs $1 billion to $2 billion dollars. Only the very largest banks and the US Government can afford to lend that kind of money to one customer. The Obama administration agreed to guarantee up to 75% of the cost of some of the proposed large new solar installations. This helped several large deals get funded and off the ground. However, in order to satisfy the requirement that the loan would in fact be paid off, government "due diligence" significantly delayed quite a few projects. But by in large, the Obama loan guarantee program was very successful.
According to the World Energy Investment Report released by the International Energy Agency, global energy investment is expected to reach approximately US$2.8 trillion by 2023. Investment in the solar energy industry is expected to surpass oil for the first time in 2023, reaching US$380 billion, while investment in oil production is expected to be US$370 billion. This suggests that the gap between investment in clean energy and investment in fossil fuels will grow wider.
In Greece, which is rich in solar energy resources, the average annual sunshine hours are about 3,000 hours, and the average annual solar radiation is 1,400-1,800 kWh/ square meter. The Greek government actively promotes solar power generation and promotes the development of the solar industry through the implementation of ecological island plans and other measures. Hellenic Petroleum invested 130 million euros to build a photovoltaic park with an installed capacity of 204 MW in Kozani, becoming one of the largest solar power projects in the Eastern Mediterranean.
The Asia-Pacific region is expected to dominate the solar energy market during the forecast period as countries such as China, India, and Japan implement ambitious renewable energy targets and support policies such as feed-in tariffs, renewable portfolio standards, and subsidies for solar installations. In addition, some countries in the Asia-Pacific region have embarked on ambitious large-scale solar projects, such as China's utility-scale solar installations, which have increased the region's cumulative installed solar capacity and made it a dominant player in the global solar market.
However, rapid growth also faces a series of opportunities and challenges. According to the latest report, the world is actively expanding solar energy production capacity to meet the growing demand for green energy. While lower prices are good for consumers, they could lead to lower investment, raising the risk of future supply shortages. In particular, the demand for key minerals such as copper, lithium, nickel, cobalt, graphite, rare earths, etc. This is crucial for the production of solar cells.
World Wide PV Solar Growth
As can be seen from the chart (updated in July 2018) the solar industry has seen remarkable growth. The red bars represent the "annual" amount of PV solar systems installed by manufacturers in giga-watts (1 GW = 1 billion watts). For reference purposes, one nuclear reactor produces about 1.3 GW of electricity per year. The data for 2012 and 2013 is from the European Photovoltaic Industry Association (EPIA). The data for 2014 and 2015 is from Mercom Capital. The data for 2016 and 2017 is from CleanTechnica. The author created the overall graph.
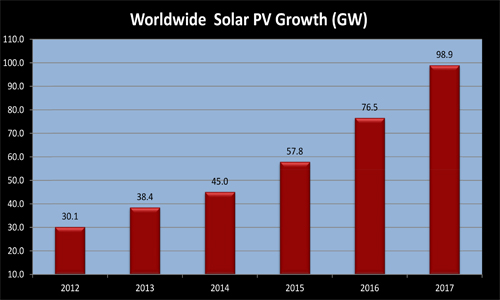
The 5 year average growth rate from 2012 (30.1 GW) to 2017 (98.9 GW) was 29% per year - a very nice growth rate. The growth in 2015 was 28%, 2016 was 32%, and 2017 was also 29%. The overall 29% growth was mainly due to China and the US, which have grown nicely throughout this five year period.
The growth in 2014 of only 17% was because of sharp cutbacks in Germany and Italy. Also, China had no growth at all as they were consolidating their tremendous leap from the previous year. However, in 2016 China doubled to 34.5 GW - by far the largest yearly installation ever. In 2018 and afterward, the long-term growth rates are expected to be roughly 20% per year. While the overall five year growth rate is very impressive, the 98.9 gigawatts of new solar in 2017 was just 0.4% of the worldwide amount of electricity (25,551 GWh) generated by all sources. There were about 417 GW of cumulative PV solar installed worldwide at the end of 2017 compared to 318 GW at the end of 2016.
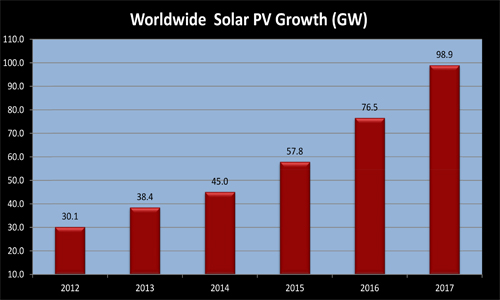
The installed PV base is roughly 20% residential rooftops, 20% commercial buildings like hotels and malls, and 60% utility plants connected to the grid. The utility market has really taken off in the last several years and is the market segment that has been the most influential in recent growth rates. The utility market is also the most cost-efficient segment as material, land, and labor costs can be spread over huge quantities.
Solar-generated electricity makes a substantial contribution during the time of day when lots of electricity is most needed, those hot summer afternoons when air conditioners are running almost constantly. This is when solar can add significant contributions to the grid at less cost than other sources. When you also throw in the pressure to go "green", you can see why the long-term future for this industry is very good.
PV Solar Installation by Country
Country | 2013 | 2014 | 2015 | 2016 |
China | 11 | 10.6 | 17 | 34.5 |
Japan | 6.9 | 9.7 | 9.5 | 8.6 |
United States | 4.8 | 6.2 | 8 | 14.6 |
UK | 1.5 | 2 | 3 | 2 |
India | 1.1 | 0.9 | 2.2 | 4 |
Germany | 3.3 | 2 | 1.9 | 1.5 |
ROTW | 9.8 | 13.6 | 16.2 | 11.3 |
Total Market | 38.4 | 45 | 57.8 | 76.5 |
The chart shows PV solar installed by the country in megawatts. Germany, back in 2012, had been the leader in solar power. Germany has a goal to discontinue all nuclear power by the year 2022 and replace it with renewable resources. However, as the price of solar power has decreased and Germany has been on target to meet its goals, they reduced their solar incentives. This prompted installations to peak in 2012 and fall off dramatically thereafter. (The same thing occurred in Italy from 2012 to 2015, not shown in the chart). In 2013 China, which has about 65% of the world's solar manufacturing capacity, began to focus on its own internal needs for clean power. It dramatically increased its solar power in 2015 and 2016. China is now the world leader in PV solar and will likely remain so for the foreseeable future. In the last several years the United States has come on strong with significant installations.
As can be seen in the chart above, the US previously had been behind in installations. In 2006 the US implemented the Renewable Energy Investment Tax Credit (ITC) which allows solar installations to apply 30% of the cost of design and installation as a federal tax credit with no maximum credit limit. The ITC was set to expire in 2016 (a 10 year program) but has been extended until 2021. In addition, a “commence construction” feature was added, effectively extending the policy through 2023.
There are 14 US States and the District of Columbia that regulate retail electricity markets in which customers may choose "alternative" power suppliers. States, such as California and Arizona, have implemented their own aggressive incentive programs to encourage alternative power. A "net-metering" type of arrangement has been implemented by California, Arizona, and many other states, whereby solar electricity is "sold back" to the utility. However, the total annual amount sold back to utilities can not exceed the customer's annual electricity usage times the purchase price.
Feed-In-Tariffs
Germany's nuclear reduction goal prompted a government policy called feed-in tariffs (FITs). A feed-in-tariff is a policy designed to encourage the adoption of renewable energy of all kinds to accelerate the reduction of the cost of renewables down to grid parity or less. Besides PV solar they include other technologies such as concentrated solar power (CSP), wind, and geothermal. FITs typically include three provisions:
- Guaranteed grid access.
- A long-term fixed purchase price contract (generally 20 years) for the electricity produced.
-
Declining contract prices for new installations that are based on the cost of renewable energy generation with a downward trend toward grid parity.
In almost all of Africa, Pakistan, Hawaii, Italy, and large portions of Japan, the price of electricity is already in excess of what the cost of electricity is from solar. Therefore in these locations, there is a ready market for today's solar electricity without any subsidies. As the price of solar electricity continues to come down every year, more and more locations will benefit from making the switch to solar when new capacity is added.
Overcapacity Issues: 2011 to 2013
Between 2007 and 2011 the solar industry grew approximately 70% per year. In particular, from the major recession year of 2009 and the recovery year of 2010, the industry grew at an incredible 172%! Production was hard-pressed to keep up with demand. As a result, companies that were able to dramatically increased capacity and gained market share. No one wanted to be left out because of a lack of capacity. So every company added capacity as fast as they could, thinking the industry growth would continue for the foreseeable future. In 2010 industry analysts warned that too much capacity was being brought on stream. However, the market was growing at double the analyst's forecasted growth rate, so the added capacity was easily absorbed. Producers felt they were "smarter than the analysts"!
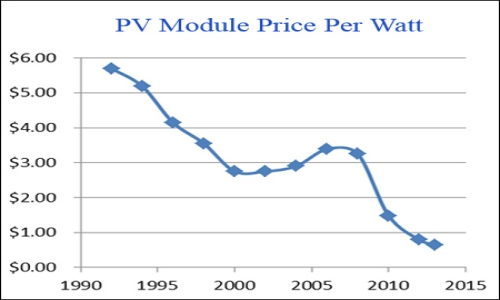
In early 2011 capacity additions finally began to exceed demand. Prices of crystalline silicon solar cells began to tumble as companies, especially second and third-tier companies, fought to reduce inventories that were piling up. In spite of the fact that the industry continued to grow at a 40% clip, there was so much inventory by the middle of the year that all prices - modules, cells, wafers, and polysilicon - tumbled uncontrollably.
For example, silicon wafer prices dropped about 70%, solar cells dropped about 60%, and modules dropped about 50%. GTM Research estimates that 31 GW of crystalline solar cells were produced. However, only about 25 GW of silicone cells were sold, leaving 6 GW of excess crystalline inventory, which was about 24% of the amount sold. Because of this glut, many smaller producers simply suspended manufacturing operations and one major company, Q-Cells of Germany, filed for bankruptcy. In the longer run the analysts were right.
The hardest hit were the polysilicon suppliers. Prices dropped from about $80/kg at the beginning of 2011 to about $20 at the end of 2011, a 75% drop. This happened because back in 2007 and 2008 there was a worldwide polysilicon shortage and polysilicon prices increased to about $400/kg. Suppliers made a lot of money and added tons of capacity so that there was a huge polysilicon capacity overhang estimated to be 40 GWs. The main reason crystalline silicon "cell" prices dropped by 60% in 2011 was because the raw material, polysilicon, which makes up a very significant part of the total cost, dropped so tremendously. While there was too much solar cell and module capacity, it was nowhere near as bad as polysilicon. Analysts believe solar cell and module capacity became reasonably in line by 2015, but the polysilicon glut took several more years to work off. As a result of falling prices while unit shipments increased, almost all companies in the solar industry were unprofitable from 2011 to 2013.
Those Chinese companies who had stock traded on American exchanges, and had to follow American accounting rules, mainly lost money because of inventory write-downs and other asset impairment write-downs. Most of these were non-cash items on balance sheets. Actual cash flows were not as negative as profits. Some companies even continued to have a positive cash flow. 2014 proved to be a profitable year for the companies that survived the 2011 through 2013 glut of products. This process was a good lesson that was learned by the entire industry.
Market Share by Technology
As can be easily seen from the chart, crystalline silicon dominates the solar market by a large margin. Thin film's share for all thin film technologies was about 7% in 2017 down from 18% in 2009. Crystalline Silicon's share has been rapidly increasing the last few years as Chinese manufacturers have come on strong.
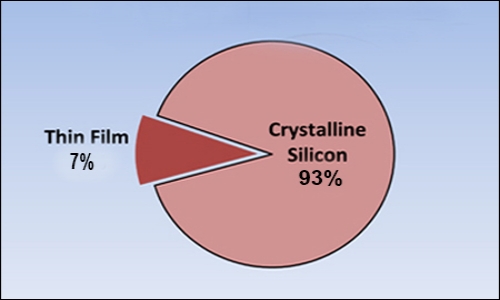
The leader by far in thin film technology is First Solar whose cadmium telluride module manufacturing costs are somewhat less than those of most crystalline cell manufacturers. Crystalline wafers are about 200 microns (a micron = one millionth of a meter) thick. In contrast, thin-film panels are made by vacuum depositing several layers of semi-conductor materials only a few microns thick. Silicon in its pure form (99.9999% pure for solar applications) is very expensive and makes up about 20% to 25% of the cost of crystalline panels vs. the semiconductor cost of about 2% in thin film panels.
There are two types of crystalline silicon, mono-crystalline and multi-crystalline. The efficiency of thin film and multi-crystalline silicon are roughly the same. However, thin film panels are currently not as efficient as mono-crystalline panels, and therefore more thin film panels are required to generate the same amount of electricity. A thin film installation can take up to 25 percent more space (and land) to achieve the same total power output as a mono-crystalline installation. But, mono-crystalline panels are significantly more expensive than thin-film. This makes thin film strongest in the utility-scale market because the cost of panels outweighs the cost of land and labor in this market. First Solar, Sharp, and a few other manufacturers have had success with "thin film" in the utility market.
Chinese suppliers using multi-crystalline silicon have significantly reduced their costs and prices, and thus have gained market share. They operate on very thin margins and depend on large volumes to get their unit costs down. Of the ten top PV producers in 2017, nine were Chinese. The dramatic drop in silicon module prices from 2011 to 2017 has probably closed the cost gap between multi-crystalline silicon and cadmium telluride.
2017 Top 10 Solar PV Manufacturers Worldwide
Listed below are the top ten PV manufacturers for 2017. Companies are ranked by "megawatts shipped", not revenue. Nine of the top 10 PV producers are purely Chinese. During 2017 approximately 60% of all PV solar panels shipped were manufactured in China. (Note that Canadian Solar has a 500 MW manufacturing plant in Canada in addition to its main plant in China.) Jinko Solar is number one on the top 10 list, followed by Trina Solar and Canadian Solar. In the past three years, JinkoSolar, Trina Solar, and Canadian Solar have been the top 3 module suppliers in the solar industry, and by some margin. These companies offer something that no other module suppliers have: "global brand recognition".
Rank | Company | Technology | Country |
1 | Jinko Solar | c-Si | China |
2 | Trina Solar | c-Si | China |
3 | Canadian Solar | a-Si, c-Si | China |
4 | JA Solar | c-Si | China |
5 | Hanwha Q-Cells | c-Si | Multiple |
6 | GCL-Sl | c-Si | China |
7 | LONGi Solar | c-Si | China |
8 | Risen Energy | c-Si | China |
9 | Shungfeng | c-Si | China |
10 | Yingli Green | c-Si | China |
Most companies try to completely vertically integrate, i.e. manufacture all three stages of production - wafers, cells, and modules. Wafer companies moved into cells because they have a cost advantage using their own wafers. Pure cell manufacturers have moved into modules, which are basically low-tech assemblies, but it also gives them a low-cost material advantage. Major players want to be totally integrated from wafers to modules and even end-user sales and installation. Having an internal supply of materials shields companies from the up-and-down swings of the spot markets and provides an opportunity to "brand" their products.
US PV Market Growth
This is the annual US PV solar installations in megawatts (MW). Note that during 2016 installations totaled 14,600 MW, a gigantic 83% increase from 8,000 in 2015.
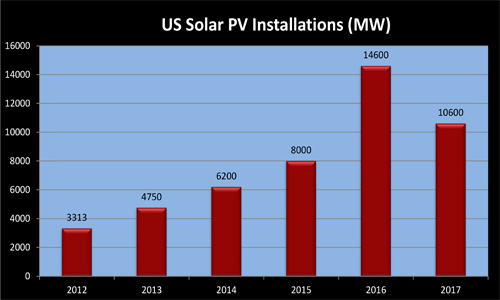
As mentioned above, the ITC (Renewable Energy "Investment Tax Credit") was set to expire at the end of 2016 but during 2016 it was extended until 2021. Many organizations rushed their solar installations to take advantage of the ITC before the end of 2016. Therefore some of the installations scheduled for early 2017 were finished in 2016.
For a more balanced calculation of the five year growth rate, the average for both 2016 and 2017, i.e. 12,600 MW, was used for the ending year of 2017. The five year annual growth rate from 2012 to 2017 was 31% using the 12,600 MW average for 2017.
US solar installations have grown dramatically in the last few years as utilities have come on strong. Until about 2011, US utility installations had been weak compared to Germany, Italy, or China due to the lack of support from the US Federal Government in the early 2000s. The planning and licensing for a large utility installation takes a minimum of two to three years plus the time to install it. So the Investment Tax Credit (ITC) tax incentive program passed in 2006 took a while to have an effect. Also, in recent years, state governments added their support and those results began to show starting about 2013.
A 100 MW to 250 MW solar installation costs $1 billion to $2 billion dollars. Only the very largest banks and the US Government can afford to lend that kind of money to one customer. The Obama administration agreed to guarantee up to 75% of the cost of some of the proposed large new solar installations. This helped several large deals get funded and off the ground. However, in order to satisfy the requirement that the loan would in fact be paid off, government "due diligence" significantly delayed quite a few projects. But by in large, the Obama loan guarantee program was very successful.
Post a Comment:
You may also like:
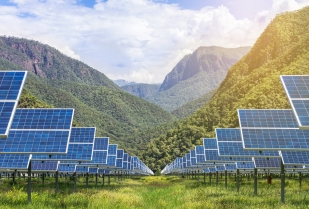
Category
Featured Articles
Expanding Research on Solar Energy ...
The application fields of solar energy are very wide, covering many fields such as the photonic industry, new energy photothermal ...
Exploring Concentrated Solar Power ...
Concentrated Solar Power (CSP) systems use very different technology than photovoltaic systems. CSP systems use the sun as the ...
Solar Cell Manufacturing Process
Solar cells are made of various materials, the most common of which include silicon, indium gallium, cadmium selenide, etc. These ...
The Evolution of Grid Electricity ...
"Electricity" cannot be stored on the grid; generation must be approximately equal to consumption at all times. However, ...
Solar Activity: Sunspots, Magnetism & ...
Solar activity refers to a series of complex phenomena in the solar atmosphere, including sunspots, flares, prominences, coronal ...